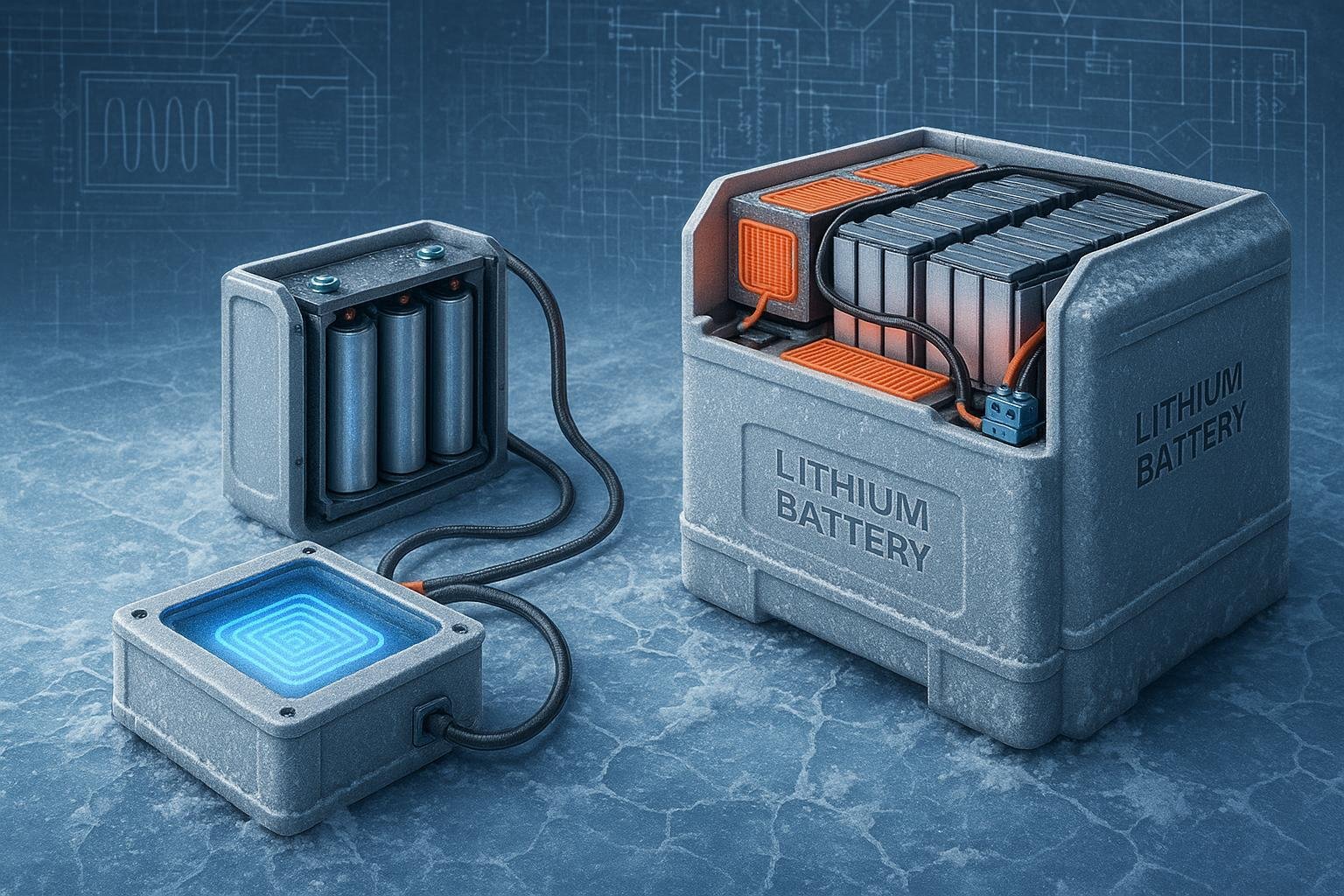
Introduction: Why Low-Temperature Performance Matters
In critical B2B industries—from telecom and smart grids to electric vehicles (EVs) and industrial automation—lithium batteries often face low-temperature environments that dramatically reduce capacity, impair safety, and threaten operational reliability. Subzero exposure can cause capacity retention to plummet by over 50%, and improper charging below freezing can result in permanent cell damage or catastrophic failure (NREL 2025). As regulatory standards become stricter and downtime costs escalate, adopting robust best practices for low-temperature battery performance is now a vital differentiator for engineering and procurement teams.
This guide provides a comprehensive, standards-backed checklist to maximize lithium battery safety, lifetime, and cost-effectiveness in climates as low as -20°C, drawing on real-world data, international compliance, and advanced engineering protocols.
Low-Temperature Performance Best Practices
1. Integrate Active Battery Thermal Management and Heating Protocols
Actively maintaining battery temperature within the optimal range (15°C–35°C) is proven to reduce capacity loss and prevent safety hazards in subzero environments. This is especially critical for large-format systems in EVs and industrial equipment (NREL 2025).
How to Implement:
- Install heating pads or Peltier films directly onto cell modules, interfaced with the BMS for pre-heating below 0°C.
- For high-demand applications, deploy liquid-cooling with integrated heating coils or heat pipes to achieve fast, uniform temperature recovery.
- Encase battery packs in insulated, heated enclosures for stationary or remote field deployments (e.g., telecom, grid backup).
Impact: Heated/heated-and-insulated systems extend cycle life 2x or more versus passive setups in peer-reviewed field tests. Failure rates and unplanned downtime are reduced substantially in harsh outdoor scenarios.
2. Enforce Industry-Standard Certification and Laboratory Testing (IEC 62660, UL 2580, UN 38.3)
Strict adherence to global battery standards is non-negotiable for safety, reliability, and cross-border compliance. Standards mandate cycle testing, abuse scenarios, and consistent performance verification at both subzero and high temperatures (Grepow).
How to Implement:
- Require suppliers to certify all modules under IEC 62660, UL 2580, and UN 38.3, including cold-climate operational and abuse tests.
- Regularly verify cycle life, swelling, and thermal failure thresholds at -20°C, -10°C, 0°C, and +20°C as per published protocols.
Impact: Ensures zero compromise on safety and reliability. Facilitates international OEM and regulatory approvals.
3. Specify Advanced Electrolytes and Interface Engineering (FEC/LiFSI/Polymer Electrolytes)
Low-temperature performance is largely determined by electrolyte conductivity and solid electrolyte interface (SEI) stability. Modern additives (fluoroethylene carbonate, LiFSI) and advanced solid/quasi-solid polymer electrolytes keep ionic resistance low and limit lithium plating at temperatures down to -20°C (ScienceDirect).
How to Implement:
- Source cells using specialty low-temp electrolyte formulations or quasi-solid-state electrolytes for applications below -10°C.
- For custom designs, consult cell vendors on latest SEI-stabilizing additives or polymer blends.
Impact: Experimental pouch cells (QSPE/NMC811) achieved >60% capacity retention at -20°C over 200+ cycles—double that of conventional electrolyte cells (PMC study, 2024).
4. Deploy Intelligent Battery Management Systems (BMS) with Low-Temperature Protection
A sophisticated BMS prevents unsafe charging/discharging, dynamically manages heating, and logs environmental data for predictive maintenance (Renogy).
How to Implement:
- Require BMS platforms to block charging below 0°C and activate pre-heating functions.
- Use BMS-integrated sensors to continuously monitor and record cell/module temperatures.
- Implement AI/predictive algorithms for heating control and anomaly detection in industrial or fleet scenarios.
Impact: Firms adopting AI-enhanced BMS have cut battery-related field failures and cold-start issues by up to 75% in recent deployments (NREL field data).
5. Adopt Insulated and Heated Battery Enclosures for Field Systems
For outdoor, telecom, grid, or remote deployments, battery enclosures with integrated insulation and programmable heating are essential to maintain cell temperature above freezing.
How to Implement:
- Specify commercial-grade battery cabinets with active heating; select insulation materials with proven R-values and low moisture ingress.
- Integrate enclosure sensors into site monitoring for real-time alerting and temperature compliance reporting.
Impact: Case studies demonstrate that insulated/heated enclosures can maintain >95% of rated cycle life during winter seasons, compared to <60% without such measures (NREL, Grepow).
6. Implement a Rigorous Cold-Weather Operation Protocol and Checklist
Standardized operating and maintenance protocols minimize the risk of cold-weather-induced failure, improve safety, and optimize ROI.
Recommended Checklist:
- Preheat batteries to >0°C before initiating charge or heavy discharge cycles.
- Avoid rapid charging/discharging below freezing; employ manufacturer-specified current limits.
- Schedule regular inspection of insulation integrity, cable harness heating elements, and BMS logs throughout the winter.
- For new deployments, require on-site validation at subzero operation per IEC/UL routines.
Impact: A documented, repeatable protocol supports regulatory audits, smoothens commissioning, and reduces troubleshooting time.
Data Snapshot: Capacity Retention by Chemistry at -20°C
Battery Chemistry | Capacity Retention at -20°C | Typical Cycle Life at -20°C |
---|---|---|
LFP (with advanced electrolyte/heating) | 60–70% | 300+ cycles |
NCA/NMC (QSPE, additivized) | 55–65% | 200+ cycles |
Standard LCO/NMC (no mitigation) | <30% | <100 cycles |
Summary & Call to Action
Applying these scientifically validated best practices—integrating advanced heating, adopting intelligent BMS, specifying certified and engineered materials, and enforcing standardized cold-weather protocols—will dramatically improve battery reliability, safety, and ROI in subzero climates. As industry trends shift towards stricter compliance and predictive, AI-driven management, staying at the forefront of low-temperature performance is no longer optional—it is a business imperative.
Next Steps:
- Conduct a full audit of your battery systems against the above checklist.
- Insist on documentation of IEC/UL/UN compliance, BMS features, and integration of advanced materials for all future procurements.
- Download authoritative guides on low-temperature battery management from NREL and consult reliable engineering sources such as Grepow’s cold-weather blog for specialized application advice.
For further technical depth or scenario-specific recommendations, explore peer-reviewed journals and up-to-date standards documentation, or consult with system integration experts.