1.What are the three materials that constitute a ternary lithium battery?
The positive electrode material of a lithium battery generally consists of lithium carbonate, lithium iron phosphate, lithium manganese oxide, and nickel-metal hydride batteries; the negative electrode material generally consists of the positive electrode of nickel-metal hydride batteries and the negative electrode of nickel-cobalt batteries; the separator generally consists of polypropylene; and the electrolyte generally consists of mineral oil and solvents. The stability of battery performance is ensured through different structures of electrode materials and electrolytes. The electrode material is a polymer compound (such as polyacrylonitrile), which has a high specific surface area and chemical activity, while the electrolyte is a liquid mixture that exhibits good chemical stability, electrolyte flow, and is easy to control viscosity and acidity. Separators can be divided into microporous separators and honeycomb separators. Microporous separators are generally used in lithium-ion battery packs, honeycomb separators are used in electric vehicle battery packs, and honeycomb separators are used in capacitor packs in car charging battery packs.
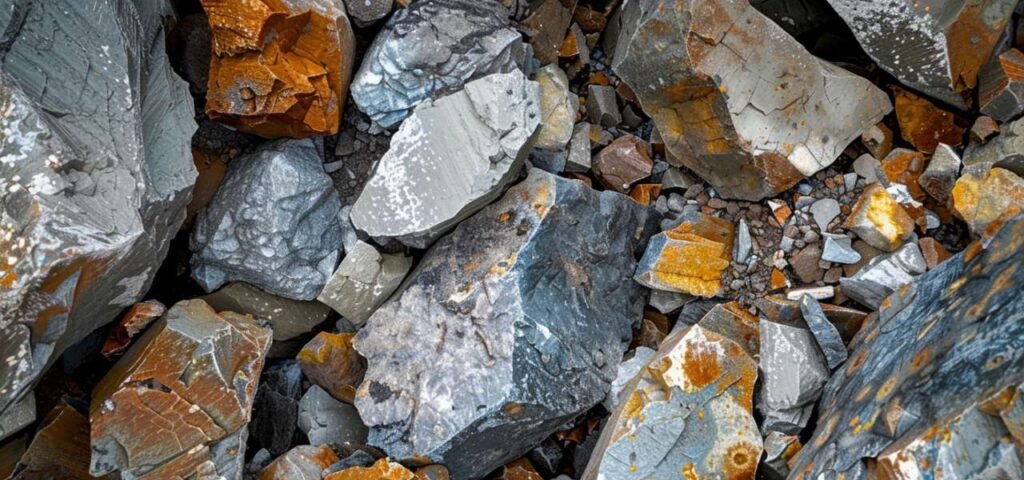
2.Structural Characteristics of Ternary Lithium Batteries
Ternary lithium batteries use lithium metal as the positive electrode material and employ an NCA/NCA structure. Its structural feature is the use of metallic lithium instead of NCA material on the negative electrode. As the positive electrode material is the most important component of ternary materials, it occupies the largest space, while the negative electrode material serves a protective role. The battery shell is also installed at the bottom of the battery pack, mainly composed of a casing and a separator. The separator contains silicon alkoxide crosslinking agents, which separate the positive electrode layer and facilitate charge exchange with the negative electrode side, thus, the performance of the separator greatly affects the battery’s capacity and safety. Additionally, lithium metal is an excellent conductor with good thermal conductivity. It’s crucial for ternary lithium batteries to form a firm and insoluble protective film between lithium ions and metallic lithium molecules.
Due to its highest energy density and cost (utilizing the most precious metal cobalt), lithium cobalt oxide (LCO) is mostly used in consumer electronics where battery price sensitivity is low.
In the field of power, from 2009 to 2016, lithium iron phosphate (LFP) dominated in passenger cars (less than 9 seats) and commercial vehicles (9 seats and above, or primarily for freight purposes) due to its low cost and high safety.
After 2016, with increasing demands for high energy density batteries in consumer vehicles and policies favoring such batteries, ternary materials emerged in passenger cars, while commercial vehicles continued to rely mainly on LFP.
In energy storage, foreign markets mainly use ternary materials, while domestically, lithium iron phosphate is primarily used, especially recycled lithium iron phosphate. With the maturity of domestic lithium iron phosphate (LFP) battery technology, cost reduction, and verified safety, domestically produced LFP gradually penetrates the global energy storage market.
3.The Four Major Materials of Lithium Batteries
Lithium-ion batteries represent modern high-performance batteries, consisting of positive electrode materials, negative electrode materials, separators, and electrolytes as the four main components. High energy density, long life, and reliable safety are required for performance.
The domestic electrification supply chain is well-established, and the landscape is clear. In 2019, Chinese enterprises accounted for 77% of the CR4 in the power battery/positive electrode/negative electrode/separator/electrolyte industries, respectively, indicating clear industry leaders in each subfield.
(1) Positive Electrode Materials of Lithium Batteries
In recent years, the booming production and sales of new energy vehicles in China have driven the rapid development of the entire upstream and downstream industry chain, especially the increasing demand for power batteries. As power batteries account for about 30-40% of the manufacturing cost of new energy vehicles, to make new energy vehicles more competitive in price and gain sufficient market competitiveness, it’s crucial to reduce the cost of power batteries. Among the constituent costs of power batteries, the cost of positive electrode materials exceeds 40% (equivalent to about 16% of the entire vehicle), so reducing the cost of positive electrode materials is critical.
Statistics show that in 2020, the total production of the top four positive electrode materials in China was 519,000 tons, a year-on-year increase of 20.8%, with lithium iron phosphate materials performing strongly, reaching a production of 142,000 tons, a year-on-year increase of 45.7%. The production of lithium cobaltate and lithium manganese oxide positive electrode materials was 73,800 tons and 92,900 tons respectively, with year-on-year increases of 24.8% and 21.6%; the production growth rate of ternary materials was the slowest, only 7%, with a total annual output of 210,000 tons.
In the first quarter of 2020, there were 17 positive electrode material manufacturers that achieved supply, a decrease of 7 compared to 2019, indicating that industry reshuffling has begun, with small enterprises with poor production capacity, technology, and customer structure starting to exit the market, and concentration is expected to increase.
Positive electrode materials are one of the key materials that determine the performance of lithium-ion batteries and are also the main source of lithium ions in commercial lithium-ion batteries. Their performance and price significantly affect the energy density and performance of lithium batteries. Currently, successfully developed and applied positive electrode materials mainly include lithium cobalt oxide, lithium iron phosphate, lithium manganese oxide, and ternary materials (nickel cobalt manganese lithium, lithium nickel oxide), with the mainstream positive electrode materials for lithium batteries in China being lithium iron phosphate and ternary materials.
Lithium cobalt oxide has a high cost and short lifespan, mainly used in 3C products; lithium manganese oxide has low energy density and a short lifespan but low cost, mainly used in special vehicles; lithium iron phosphate has a long lifespan, good safety, and low cost, mainly used in commercial vehicles; ternary materials, especially NCM, have high energy density, good cycling performance, and long lifespan, mainly used in passenger vehicles.
Many ternary battery companies are concentrating on the research and development of high-nickel ternary batteries. Although ternary lithium batteries are slightly inferior to lithium iron phosphate batteries in terms of safety and stability, they have advantages in energy density, low-temperature resistance, and range that other batteries cannot match.
Positive electrode materials need to have the following characteristics:
A.Have a high redox reaction potential to achieve high output voltage of lithium-ion batteries;
B.High lithium content, high material stacking density, resulting in high energy density of lithium-ion batteries;
C.Good structural stability during chemical reaction processes, resulting in long cycle life of lithium-ion batteries;
D.High conductivity, resulting in good charge and discharge rate performance of lithium-ion batteries;
E.Good chemical stability and thermal stability, not easy to decompose or heat, resulting in good safety of lithium-ion batteries;
F.Low cost, resulting in sufficiently low cost of lithium-ion batteries;
G.Relatively simple manufacturing process, suitable for large-scale production;
H.Low environmental pollution, easy to recycle and reuse.
Currently, key indicators such as energy density, charge and discharge rate, and safety of lithium-ion batteries are mainly constrained by positive electrode materials.
(2) Negative Electrode Materials of Lithium Batteries
The negative electrode is a major component of lithium batteries, consisting of negative electrode active materials, binders, and additives mixed into a paste and uniformly applied to both sides of a copper foil, then dried and rolled.
Negative electrode materials mainly refer to negative electrode active materials. Negative electrodes can be divided into two categories: carbon materials and non-carbon materials. Carbon materials include artificial graphite, natural graphite, mesophase carbon microspheres, hard carbon, and soft carbon, while non-carbon materials include silicon-based materials, tin-based materials, and lithium titanium oxide.
4.Composition of Ternary Lithium-ion Battery Positive Electrode Materials
The positive electrode materials of ternary lithium-ion batteries mainly consist of four elements: nickel (Ni), cobalt (Co), manganese (Mn), and lithium (Li). In the general production process of positive electrode materials, the sources of various elements are nickel sulfate, cobalt sulfate, manganese sulfate, and lithium carbonate, respectively. The following sections analyze the mineral sources of these elements, their main geographical distributions, the abundance of these resources in China, and how the development of the ternary lithium-ion battery industry chain affects the demand for these resources.
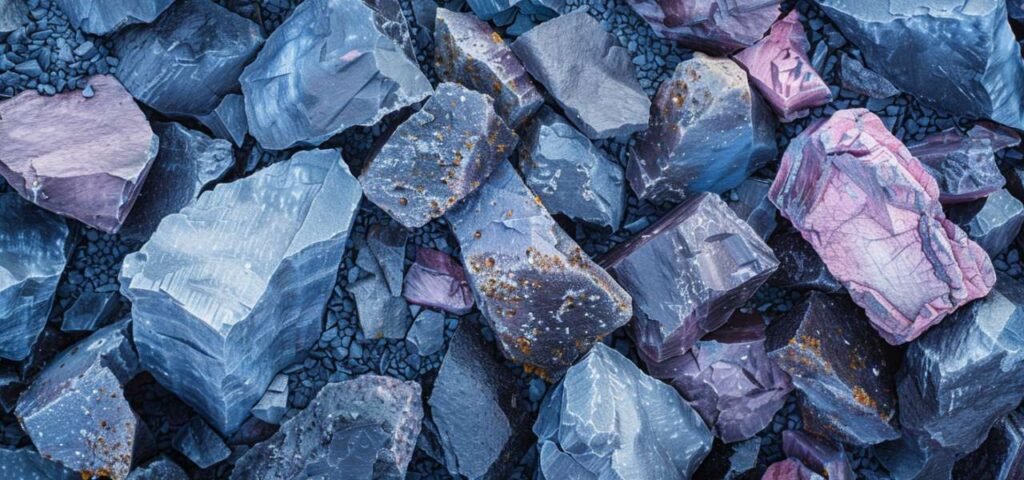
(1) Lithium Resources
Lithium ore mining and production companies mainly supply battery-grade lithium carbonate or lithium hydroxide as raw materials to manufacturers of positive electrode materials for batteries. There are four main methods for preparing lithium salts from lithium ores: lime method, sulfuric acid method and sulfate, and chloride roasting method. The main process of these four methods is to sinter lithium ores with sulfuric acid or sulfates, lime or chlorides, and then produce lithium salt products through processes such as dissolution and filtration. Currently, the mainstream lithium ore-to-lithium process adopts the sulfuric acid method.
The main raw materials for lithium ore-to-lithium are spodumene and lithium mica. Spodumene is the richest source of lithium and most conducive to industrial production. Globally, lithium-rich spodumene deposits are mainly distributed in Australia, Canada, Zimbabwe, Zaire, Brazil, and China; lithium mica deposits are mainly found in Zimbabwe, Canada, the United States, Mexico, and China.
China has excellent lithium ore-forming conditions. According to the lithium ore-forming conditions and laws, China has divided the country into 12 lithium ore-forming belt regions such as Songpan-Ganzi, Altai, North Tibet, and Qaidam, predicting the potential lithium resources (LiCl) from brine lithium mines to be 92.48 million tons, of which 52.21 million tons are within 500 meters; the potential hard rock lithium mine resources (Li2O) are 5.94 million tons, of which 4.96 million tons are within 500 meters. The predicted potential resources equivalent to metallic lithium amount to 17.6 million tons (equivalent to lithium carbonate of 93.67 million tons), with a confirmed resource rate of only 25.4%.
In 2015, the total consumption reached 78,700 tons of lithium carbonate equivalent, accounting for 37.2% of the world’s total. In that year, in China’s lithium product consumption, batteries accounted for 50.9%, lubricants 15.3%, glass ceramics 12.8%, pharmaceuticals 8.2%, dyes and adsorbents 5.1%, catalysts 4.2%, and others 3.5%. If we estimate the demand for lithium-ion batteries in China to be 125 GWh in 2020 (compared to 30 GWh in 2016), with half of the batteries being ternary batteries (assuming NCM523), and each kWh of ternary battery using 0.52 kg of nickel (calculated as metallic nickel), then by 2020, the amount of nickel consumed by lithium-ion batteries for power will reach 32,000 tons, a small fraction of the annual nickel consumption in the country. Therefore, it is expected that the growth in nickel demand due to lithium-ion batteries will not change the current supply-demand structure of nickel resources.
(2) Nickel Resources
Nickel ore mining and production companies mainly supply battery-grade nickel sulfate as raw materials to manufacturers of positive electrode materials for batteries. Nickel resources are found in laterite nickel ores. The main distribution of laterite nickel ores worldwide is in two regions within the tropics: New Caledonia and eastern Australia in Oceania, extending north to Indonesia and the Philippines in Southeast Asia; and the Caribbean region in Central America. Most industrially significant laterite nickel deposits are developed on top of ultramafic rocks, resulting from extensive long-term chemical weathering in tropical or subtropical regions, composed of loose clay-like ores containing iron, aluminum, silicon, and other hydrated oxides.
Australia has the largest nickel metal reserves and basic reserves in the world, accounting for 37.8% and 19.6% of the global total, respectively, with reserves concentrated mainly in Australia, New Caledonia, Russia, Cuba, Canada, Brazil, South Africa, and Indonesia, which account for 89.5% of the world’s total nickel metal reserves and 84.1% of the total nickel basic reserves. China’s nickel resources are relatively scarce, with only 9.6% of the total nickel ore reserves in the country, meaning that not only are the reserves relatively small, but the domestic laterite nickel ore grades are also relatively low, resulting in high extraction costs and a lack of competitiveness in China’s laterite nickel ores.
Currently, nickel resources worldwide are mainly used for stainless steel production, and below are the main consumption areas of nickel resources in China. If we estimate the demand for lithium-ion batteries in China to be 125 GWh in 2020 (compared to 30 GWh in 2016), with half of the batteries being ternary batteries (assuming NCM523), and each kWh of ternary battery using 0.52 kg of nickel (calculated as metallic nickel), then by 2020, the amount of nickel consumed by lithium-ion batteries for power will reach 32,000 tons, a small fraction of the annual nickel consumption in the country. Therefore, it is expected that the growth in nickel demand due to lithium-ion batteries will not change the current supply-demand structure of nickel resources.
(3) Cobalt Resources
After cobalt ore is mined, cobalt refining companies produce cobalt sulfate, which is then supplied downstream as raw materials for positive electrodes of ternary batteries. Cobalt is widely distributed on Earth but occurs in low concentrations. Cobalt mainly occurs associated with copper and nickel, with independent cobalt resources accounting for only 17%.
Pure cobalt deposits (cobalt arsenide deposits, cobalt sulfide deposits, and cobalt iron deposits) are rare worldwide. Cobalt resources are mainly associated with lateritic nickel deposits, magmatic copper-nickel sulfide deposits, and sandstone copper deposits. Lateritic nickel deposits are mainly distributed in countries such as Cuba, New Caledonia, and the Philippines within the equatorial belt; magmatic copper-nickel sulfide deposits are mainly distributed in countries such as Russia, Canada, Australia, and China; sandstone copper deposits are mainly found in the Congo (Kinshasa) and Zambia. Additionally, there are significant amounts of cobalt in manganese nodules on the deep ocean floor and seamount areas, primarily in the Pacific Ocean, representing potential resources for the future. The figure below shows the global distribution of cobalt resources. The world’s cobalt reserves are mainly concentrated in the Congo (Kinshasa), Australia, Cuba, New Caledonia, Zambia, and Russia, accounting for approximately 80% of the world’s total cobalt reserves.