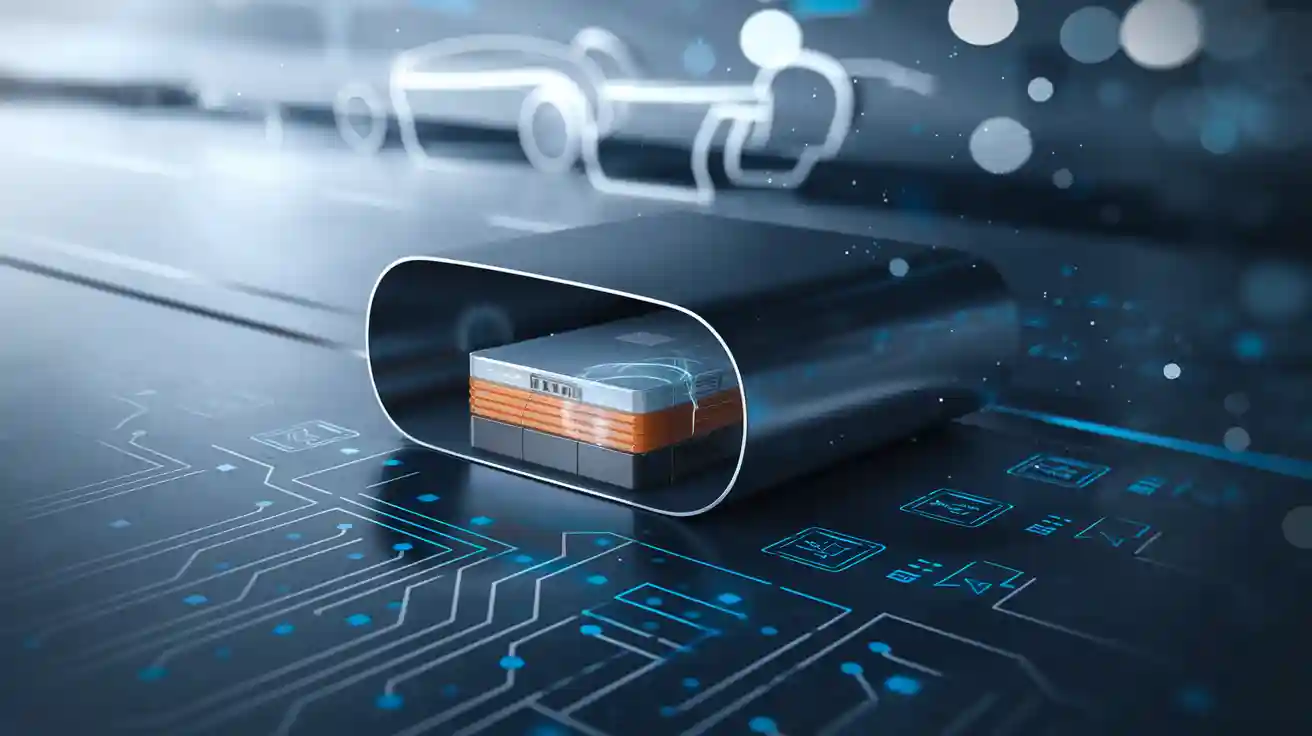
Pouch lithium-ion battery cells set the standard in 2025 by delivering exceptional energy density, lightweight structure, and flexible design. Manufacturers choose pouch cells for electric vehicles and portable electronics because these batteries maximize usable space. The table below shows how pouch cell energy density reaches 800 Wh L⁻¹, making it a top performer among lithium-ion batteries.
Cell Format | Volumetric Energy Density (2020) | Projected Energy Density (2025) | Packaging Efficiency (Module/Pack Level) |
---|---|---|---|
Pouch Cell | 600 Wh L⁻¹ | 800 Wh L⁻¹ | Moyen |
Prismatic Cell | 550 Wh L⁻¹ | 700 Wh L⁻¹ | Haut |
Cylindrique | 850 Wh L⁻¹ | >950 Wh L⁻¹ | Faible |
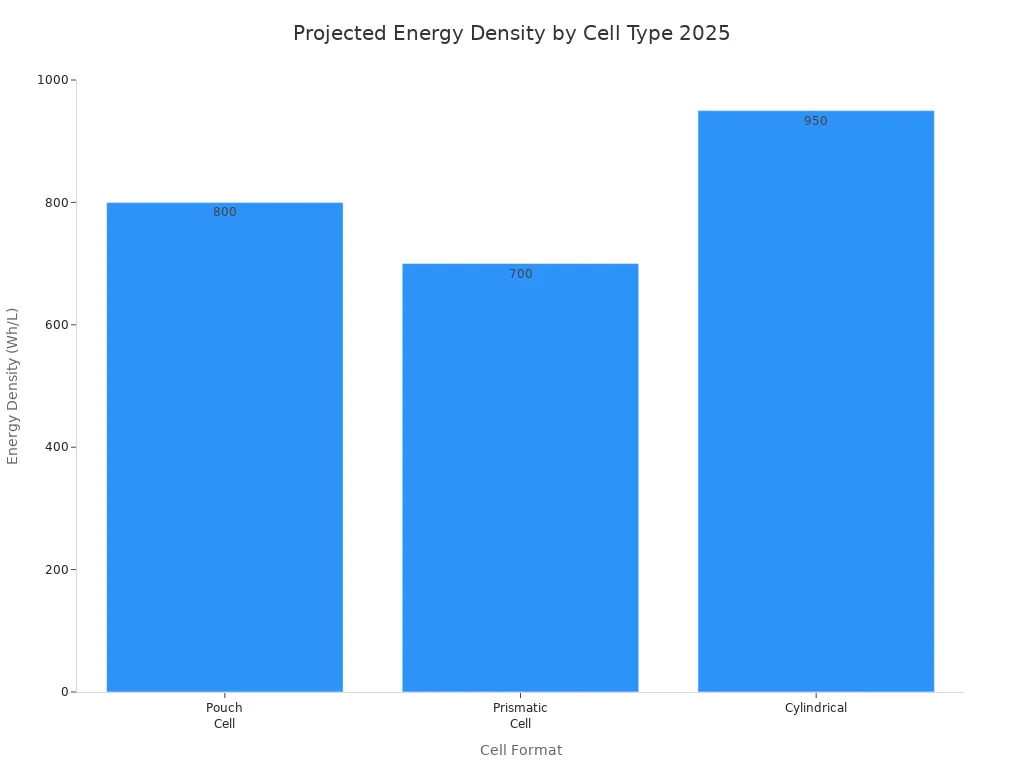
Pouch cells offer clear advantages in adaptability and packing efficiency, giving designers more options for battery layout in advanced applications.
Pouch Lithium-Ion Battery Basics
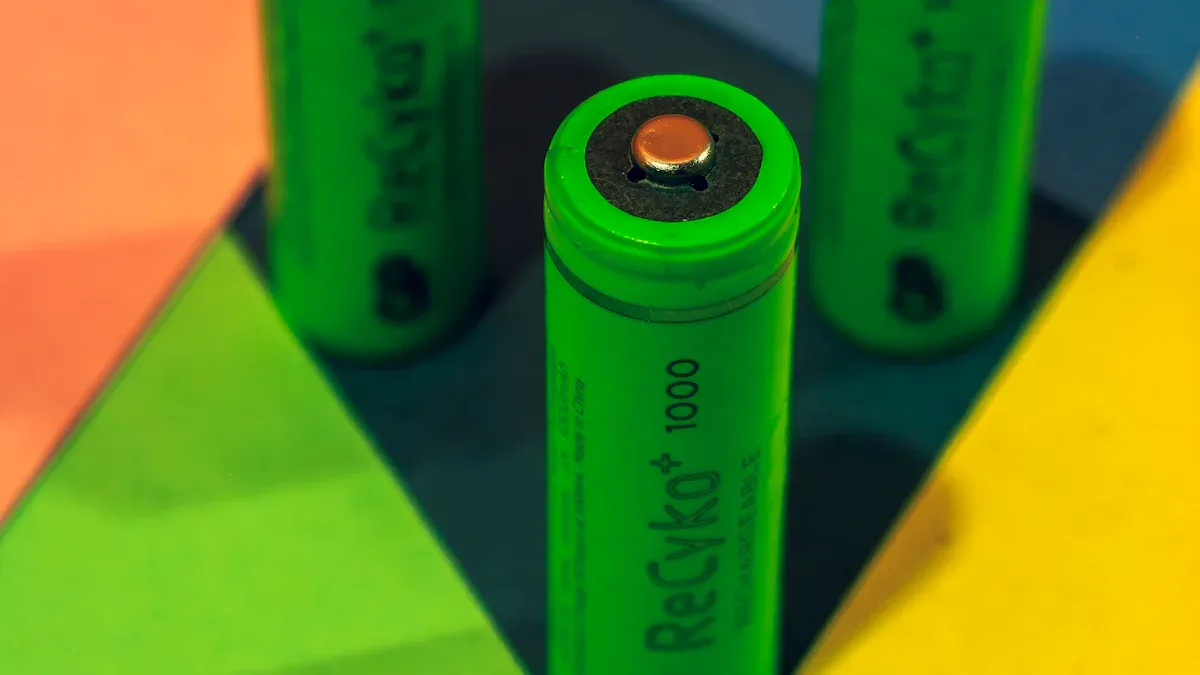
Structure and Materials
A pouch lithium-ion battery stands out due to its unique structure and advanced materials. Engineers design each pouch cell with stacked or folded layers. These layers include a cathode, anode, and separator. The pouch casing uses a laminated structure made from polymer-aluminum foil-polymer layers. This design gives the battery both flexibility and protection.
Key components of a pouch cell battery include:
- Cathode: Made from lithium cobalt oxide, lithium manganese oxide, or lithium iron phosphate.
- Anode: Usually constructed from graphite.
- Separator: A thin, porous membrane that prevents short circuits but allows ions to pass.
- Electrolyte: A liquid or gel containing lithium salt in an organic solvent, which enables ion movement.
- Current collectors: Copper and aluminum foils that conduct electrical current.
- Pouch casing: Flexible laminated foil that protects the internal lithium cells.
Manufacturers mix binding agents, active materials, and conductive materials into a paste. They coat this paste onto metal foils, dry it, and compress it to achieve the right porosity and thickness. After stacking the electrode sheets, they inject the electrolyte and seal the assembly inside the pouch. The aluminum foil provides a strong barrier against moisture and gas, while polymer films add flexibility and reduce weight. Composite materials and non-woven fabrics improve insulation and thermal management, which are important characteristics for safety and performance.
Role in Modern Applications
Pouch cell batteries power a wide range of devices in 2025. Their characteristics make them ideal for many applications. The table below highlights key areas where pouch lithium-ion batteries excel:
Domaine d'application | Description | Key Advantages of Pouch Cells |
---|---|---|
Électronique grand public | Used in smartphones, tablets, laptops for lightweight, compact, and long-lasting batteries. | Lightweight, compact design, longer battery life |
Véhicules électriques (VE) | Powers EVs to increase driving range without adding significant weight. | Higher energy density, improved performance |
Renewable Energy Storage | Stores energy from solar and wind to stabilize power supply. | Reliable energy storage, supports grid integration |
Robotics and Drones | Enhances flight time and reliability for commercial drones and robots. | Lightweight, high capacity |
Pouch lithium-ion batteries also support medical devices, aerospace, and military equipment. Their flexible design allows them to fit into irregular spaces, which is essential for portable electronics and electric vehicles. The lightweight pouch casing reduces overall device weight, improving performance and portability. Although pouch cells require extra protection at the module level, their adaptability and high energy density make them a top choice for modern lithium-ion battery applications.
Advantages of the Pouch Cell
Densité énergétique élevée
Pouch cell batteries deliver haute densité énergétique, which means they store more energy in a smaller and lighter package. Engineers achieve this by using ultrathick, high-discharge capacity cathodes and lithium metal anodes. As a result, gravimetric energy densities can exceed 700 Wh/kg. Devices such as electric vehicles and electric aircraft benefit from this feature. They can travel longer distances or operate for extended periods without increasing battery size or weight. The compact design of the pouch cell battery also supports longer operation times in mobile electronics. However, higher energy density requires careful attention to battery safety, cycle life, and thermal management. Manufacturers must balance these factors to ensure high-quality performance and reliability.
Conception légère
Les conception légère of pouch cells offers several advantages for both transportation and consumer electronics:
- Pouch cells allow smartphones and laptops to be thinner and lighter, making them easier to carry.
- The high energy density and flexible shape of the pouch cell battery support longer device usage and faster charging.
- In electric vehicles, pouch cells help create lighter battery packs, which improves driving range and efficiency.
- The flexible packaging of pouch cells enhances safety by swelling rather than exploding if a fault occurs.
- Manufacturers use innovative assembly methods with pouch cells to save space and improve efficiency in battery production.
This lightweight structure enables pouch cells to store more energy in a smaller space, which is critical for devices with strict space and weight limits.
Facteur de forme flexible
The flexible form factor stands out as one of the most important features of the pouch cell. Unlike rigid metal casings, pouch cells use a flexible, multilayered aluminum-plastic film pouch. This design allows manufacturers to create batteries in ultra-thin, curved, or custom shapes. The internal structure includes laminated electrodes and separators, which can be compacted to different thicknesses and shapes. As a result, pouch cells adapt to various product designs and space constraints. The flexible polymer casing also contributes to the high energy density and lightweight characteristics of the pouch cell battery.
Pouch cells can fit into unconventional device layouts. For example, wearable devices, compact electronics, and uniquely shaped products benefit from this flexibility. The thin, flat geometry of the pouch cell enables high stacking efficiency and reduced weight. However, this flexibility requires extra mechanical support to prevent damage and manage swelling from internal gas generation.
Packing Efficiency
Packing efficiency measures how well cells fit together in a battery pack. Prismatic cells, with their rectangular shape, achieve nearly 100% packing efficiency. Cylindrical cells reach about 90.69% due to their round shape, which leaves gaps. Pouch cells use a flexible foil-based casing, which allows for higher cell-level energy density and lower manufacturing costs. However, pouch cells tend to expand during use, which can reduce packing efficiency compared to prismatic cells. Despite this, the pouch cell’s lightweight and flexible design make it easier to fit into tight or irregular spaces, supporting efficient use of available volume in many applications.
Remarque : While pouch cells offer advantages in design flexibility and energy density, they require careful management of swelling and mechanical support to maintain the safety of the battery pack.
Caractéristiques de sécurité
Battery safety remains a top priority for pouch cell technology. The most common safety incidents include internal short circuits, often caused by mechanical damage such as indentation or puncture. These incidents can lead to rapid voltage drops and thermal runaway, which pose fire hazards. Smaller pouch cells are more vulnerable to such failures. Manufacturers address these risks with several strategies:
Safety Incident Type | Cause | Severity | Mitigation Strategies |
---|---|---|---|
Internal Short Circuits (ISCs) | Mechanical damage, component contact | Haut | Protection vents, current fuses, anode coatings, thermally stable materials, polymer microspheres |
Mechanical Stress-Induced ISCs | Indentation, puncture | Moyen | Robust packaging, improved mechanical design, silicon nanowire anodes |
Emballement thermique | Heat accumulation, ISCs | Critical | Air/liquid/phase change cooling, fire suppression, smoke detectors |
Manufacturers use aluminum-laminated casings, safety vents, and advanced materials to improve battery safety. Thermal management systems, such as air or liquid cooling, help prevent overheating. Fire suppression and smoke detection devices further enhance the safety of the battery pack. These features of the pouch cell create a multi-layered safety approach for modern lithium-ion battery applications.
Application Adaptability
The adaptability of pouch cells makes them suitable for a wide range of applications. Their flat, laminated design without a rigid casing allows them to fit easily into different installation spaces and shapes. Flexible assembly lines enable quick adaptation to various specifications, producing batteries in diverse sizes and forms. The absence of a rigid casing makes pouch cells lighter and thinner, which increases their suitability for portable electronics, electric vehicles, and hybrid vehicles. Pouch cells achieve a packaging utilization rate of 90%-95%, enabling efficient use of space. Their flexible design allows for easier integration into battery packs and systems across different device categories.
- Pouch cells adapt to various shapes and spaces in consumer electronics, electric vehicles, and renewable energy storage.
- The high energy density and cost-effectiveness of pouch cells support their use in multiple device categories.
- Compared to prismatic cells, pouch cells are less prone to explosion or fire, which enhances battery safety in diverse applications.
The advantages of the pouch cell—high energy density, lightweight design, flexible form factor, and adaptability—make it a preferred choice for next-generation lithium-ion battery applications.
Pouch Cells vs. Cylindrical and Prismatic
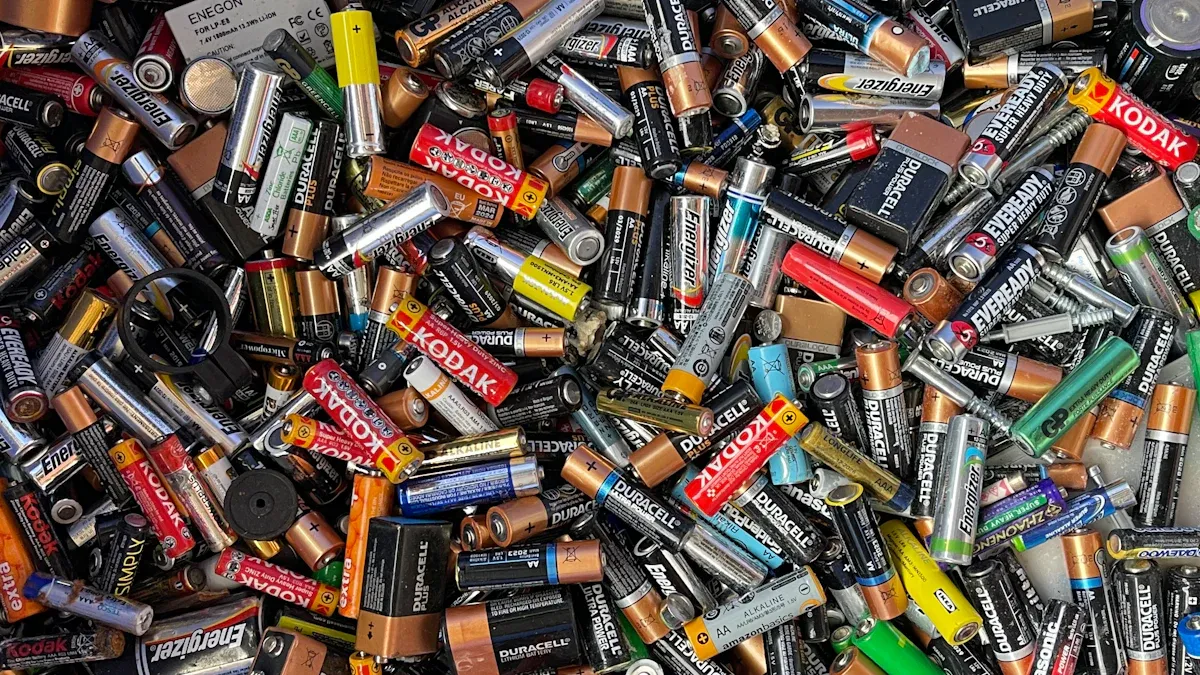
Comparaison des performances
Battery performance varies significantly between pouch cell, prismatic, and cylindrical lithium-ion battery formats. The table below highlights key differences in 2025:
Performance Aspect | Prismatic Cells | Cylindrical Lithium-Ion Battery | Pouch Cell |
---|---|---|---|
Shape & Space Efficiency | Rectangular, high space efficiency | Standardized sizes, lower pack-level energy density | Flexible shapes, thin profiles, 95% space utilization |
Densité énergétique | Up to 250 Wh/kg | ~250 Wh/L | High, custom shapes enable efficient packing |
Thermal Management | Complex, needs advanced cooling | Radial heat dissipation, 30% faster than prismatic | Controlled venting, less robust than cylindrical |
Durabilité | Durable, ideal for EVs and storage | Robust, withstands shocks, long lifecycle | Flexible, less mechanically stable |
Manufacturing Cost | Higher, complex processes | Cost-competitive, automated production | Moderate, flexible but less standardized |
Prismatic cells excel in space efficiency and energy density for large-scale applications. Cylindrical lithium-ion battery cells offer superior thermal management and mechanical durability, making them popular in consumer electronics. Pouch cell batteries provide high design flexibility and space utilization, but require careful management of swelling and mechanical support.
Design Differences
Design sets each cell type apart. Pouch cell batteries use a flexible aluminum-plastic film, making them lightweight and adaptable to custom shapes. Cylindrical lithium-ion battery cells have a rigid metal casing with spiral-wound electrodes, providing strong mechanical protection and efficient heat dissipation. Prismatic cells feature a flat, rigid casing with stacked electrodes, balancing protection and space efficiency. The pouch cell design allows for thinner, lighter batteries, but increases vulnerability to mechanical damage and swelling. Cylindrical lithium-ion battery cells remain the most robust, while prismatic cells offer a middle ground.
Adéquation de l'application
Each cell type fits specific applications. Cylindrical lithium-ion battery cells dominate consumer electronics, power tools, and robotics due to their durability and cost-effectiveness. Prismatic cells lead in electric vehicles and grid storage, thanks to their space efficiency and long cycle life. Pouch cells excel in wearables, premium electric vehicles, and devices needing custom shapes. However, pouch cell batteries face unique challenges, such as swelling from gas generation and the need for extra mechanical support. Designers must consider these factors when choosing the right battery for their application.
Remarque : Swelling and mechanical vulnerability in pouch cell batteries require careful system design and battery management, especially in automotive and consumer electronics.
Pouch Cell Trends in 2025
Material Innovations
In 2025, pouch cell technology benefits from major advances in materials. Companies like Nuvvon develop solid-state pouch cells that use solid polymer electrolytes instead of liquid ones. This change increases thermal stability and allows the cells to work well in temperatures from -20°C to 60°C. These new pouch cells can last over 2,000 cycles and pass strict safety tests, making them suitable for electric vehicles and other demanding uses. Gotion and ATL push the limits with high-nickel cathodes and fast-charging features, reaching energy densities up to 700 Wh/L. ATL also creates flexible pouch cell formats for different device needs. Hitachi High-Tech supports these improvements with advanced tools for quality control and research. New separators, enhanced with carbon nanotubes, help detect short circuits early and improve heat management, which keeps pouch cell performance high.
Safety and Longevity
Manufacturers focus on making pouch cell batteries last longer and work more safely. Advanced Battery Management Systems (BMS) now track temperature, voltage, and charge in real time. These systems help prevent overheating and other risks. New materials, such as fire-retardant adhesives and coatings, add extra protection by forming barriers when exposed to heat. Charging methods like pulse charging can extend battery life by up to 70%. AI-powered BMS and new testing tools spot problems early, which reduces failures. These changes lower the cost of owning devices with pouch cell batteries because users replace batteries less often and enjoy longer device life.
Integration in New Devices
Designers use pouch cell batteries to create slimmer, lighter, and more powerful products. The flexible shape of the pouch cell allows it to fit into compact and unique device layouts. Higher energy density means devices can run longer or use smaller batteries. Improved heat management helps devices stay cool, even during heavy use. However, pouch cells need extra support to handle pressure and avoid swelling. Advanced BMS features, such as real-time monitoring and cell balancing, keep devices safe and reliable. These trends make pouch cell batteries a top choice for new applications in consumer electronics, electric vehicles, and energy storage.
Pouch lithium-ion battery cells offer high energy density, lightweight design, and flexible shapes. These features make them ideal for electric vehicles, consumer electronics, and new technology. Engineers use pouch cells in ev battery packs to improve performance and save space. Designers can fit these batteries into many device types. Readers should consider pouch cells for future projects because they provide strong benefits with manageable trade-offs.
FAQ
What makes pouch lithium-ion batteries safer than other types?
Manufacturers use aluminum-laminated casings and advanced safety features. These include vents and thermal management systems. These features help prevent fires and overheating. Pouch cells also swell instead of exploding, which reduces the risk of sudden failure.
How long do pouch cell batteries typically last?
Most pouch cell batteries last between 1,000 and 2,000 charge cycles. Proper battery management and temperature control can extend their lifespan. Users should avoid deep discharges and extreme temperatures for best results.
Can pouch cells swell during use?
Swelling can occur if gas builds up inside the pouch. This usually happens due to overcharging, overheating, or internal short circuits. Battery management systems monitor and control these risks to keep devices safe.
Are pouch cells suitable for electric vehicles?
Pouch cells work well in electric vehicles. Their high energy density and flexible shape allow engineers to design efficient battery packs. Many premium EVs use pouch cells to maximize range and save space.
What are the main trade-offs when choosing pouch cells?
Advantage | Trade-Off |
---|---|
High energy density | Needs extra protection |
Lightweight | Less mechanical strength |
Flexible shape | Can swell under stress |
Designers must balance these factors for each application.