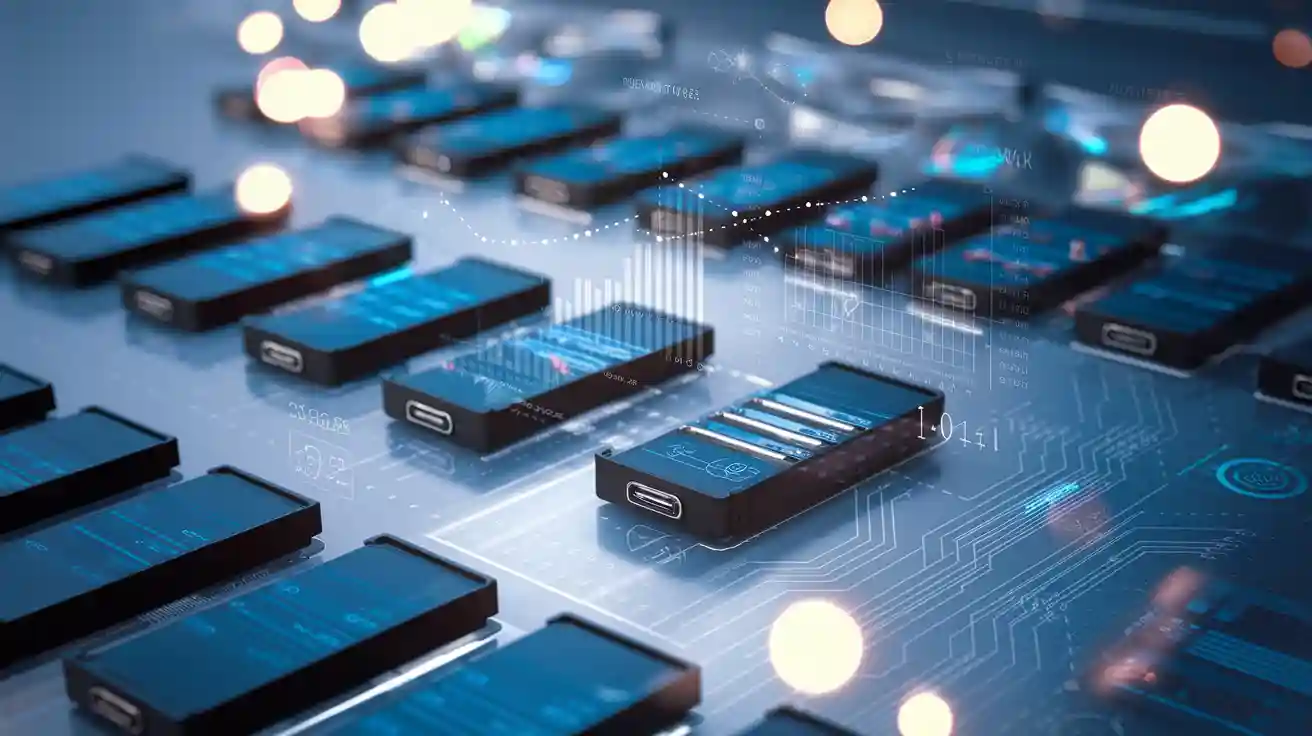
In 2025, pouch lithium-ion battery cells show strong performance because of their lightweight, flexible design and high energy density. These cells stand out in many sectors, such as consumer electronics, electric vehicles, and renewable energy storage. The pouch cell uses an aluminum-laminated case, which makes the battery lighter and allows for custom shapes. Many manufacturers choose pouch cells for their packaging efficiency, adaptability, and safety advantages. The table below displays the market share of each lithium-ion battery cell format:
Battery Cell Format | Market Share in 2025 (%) |
---|---|
Prismatique | 48 |
Cylindrique | 31 |
Pouch | 21 |
Pouch lithium-ion battery cells continue to gain popularity as their design supports high performance, safety, and market growth.
Features of the Pouch Cell
Conception légère
Pouch cells stand out for their lightweight construction. Manufacturers use a flexible, laminated foil casing made from layers of aluminum and plastic. This design removes the need for a heavy metal enclosure, which is common in prismatic and cylindrical cells. As a result, pouch lithium-ion battery cells are about 40% lighter than steel-shell lithium batteries and 20% lighter than aluminum-shell batteries of the same capacity. The internal structure stacks thin layers of cathode, separator, and anode materials on metal foils, making the cell compact and light. The absence of a rigid case means the battery compartment must provide extra support, but the weight reduction benefits many applications.
- Pouch cells use a flexible, laminated foil casing.
- The design reduces weight while keeping the cell protected.
- The flexible structure allows for various shapes and sizes.
- Pouch cells are lighter than prismatic and cylindrical cells.
Flexible Packaging
The flexible packaging of the pouch cell offers significant design flexibility. Manufacturers can create cells in almost any shape or size, including ultra-thin, curved, round, triangle, hexagon, and more. This adaptability helps fit batteries into tight or irregular spaces, which is important for devices like drones, electric cars, and portable electronics. The soft, lightweight pouch design allows for easy customization to meet specific customer needs. Experimental testing confirms that pouch lithium-ion battery cells can be produced in any desired shape, making them suitable for a wide range of applications.
Specification Aspect | Description / Impact |
---|---|
Packaging Material | Laminated aluminum-plastic film casing, lightweight and flexible |
Flexibilité de la conception | Enables thinner cells, customizable shapes and sizes tailored to customer requirements |
Adaptability | Shape can be changed to any form, facilitating new cell model development and diverse applications |
Weight Advantage | 40% lighter than steel-cased and 20% lighter than aluminum-cased lithium batteries of same capacity |
Safety Performance | High safety due to flexible packaging that swells/cracks instead of exploding |
Electrical Performance | Lower internal resistance reduces self-discharge, improves rate performance, generates less heat |
Densité énergétique | 240-250 Wh/kg for pouch cells vs. 210-230 Wh/kg for prismatic hard shell cells |
Densité énergétique élevée
Pouch cells deliver high energy density, which means they store more energy in a smaller and lighter package. In 2025, leading pouch lithium-ion battery cells reach gravimetric energy densities of up to 450 Wh/kg and volumetric energy densities of up to 1150 Wh/L. Some next-generation models even approach 500 Wh/kg and 1300 Wh/L. This higher energy density makes pouch cells ideal for electric vehicles and portable electronics, where space and weight matter most.
Type de batterie | Gravimetric Energy Density (Wh/kg) | Volumetric Energy Density (Wh/L) |
---|---|---|
Amprius Next-Generation (2023) | ~500 | ~1300 |
Amprius Commercially Available | Up to 450 | Up to 1150 |
Pouch cells also outperform prismatic and cylindrical cells in system-level energy density. The flexible design allows for better space utilization, which increases the total energy stored in a battery pack.
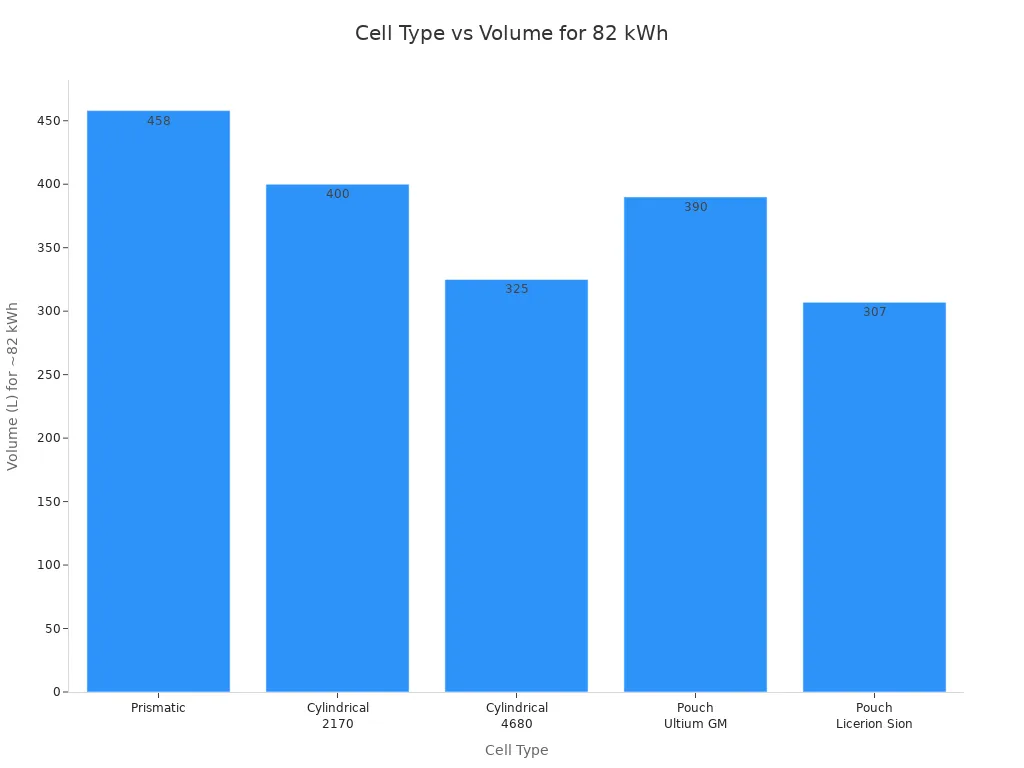
Space Efficiency
The features of the pouch cell include excellent space efficiency. The flexible, casing-free design allows pouch cells to be compressed and arranged densely, improving volumetric energy density at the pack level. Unlike cylindrical cells, which leave gaps due to their round shape, pouch cells can be stacked with minimal wasted space. Prismatic cells also offer good space utilization, but their thicker walls and complex assembly add weight and cost.
Cell Type | Packaging Characteristics | Packaging Efficiency Impact | Space Utilization Effect | Additional Notes |
---|---|---|---|---|
Pouch Cell | Laminated flexible foil pouch casing | High cell-level energy density; lower manufacturing cost | Can be compressed and arranged densely, improving volumetric energy density at pack level | Fragile; swelling 8-10% over 500 cycles affects pack design; requires compression and careful handling |
Cylindrical Cell | Rigid metal casing, cylindrical shape | Good mechanical stability; lower packaging density due to shape | Creates voids between cells, reducing space utilization | Requires support systems; better thermal management; lower packaging efficiency |
Prismatic Cell | Rectangular metal or plastic casing | Space-efficient stacking; higher manufacturing cost | Dense arrangement with minimal gaps, maximizing space utilization | Heavier than pouch; better reliability; thermal management challenges |
Note: While pouch cells offer higher energy density and better space efficiency, they require external support structures to handle pressure and swelling. This can reduce some of the space efficiency gains at the battery pack level, but the flexible design still provides significant advantages for integration in compact devices.
The advantages of the pouch cell include lightweight construction, high energy density, and flexible design. These features make pouch lithium-ion battery cells a top choice for applications that demand efficient use of space and weight.
Pouch Lithium-Ion Battery Performance
Cycle de vie
Cycle life measures how many times a pouch cell can charge and discharge before its capacity drops below a set level. In 2025, pouch cells show improved cycle life, but they still trail behind prismatic and cylindrical cells. The soft-sided pouch design allows swelling, which can limit deep cycling and long-term reliability. Manufacturers test cycle life under lean electrolyte conditions to better reflect real-world use. The table below shows the cycle life of different pouch cell types:
Sample Type | Cycle Life (Cycles) | Notes on Conditions and Performance |
---|---|---|
Bare Si-C | 237 | Cycle life plunging point under extremely lean electrolyte testing (ELET) conditions; capacity retention ~64.2% |
Si-C/PD1 Coated | 402 | Improved cycle life due to PD-based blocking layer reducing electrolyte decomposition by ~40% |
Si-C/PD2 Coated | 583 | Highest cycle life among tested samples under ELET; significant capacity retention improvement |
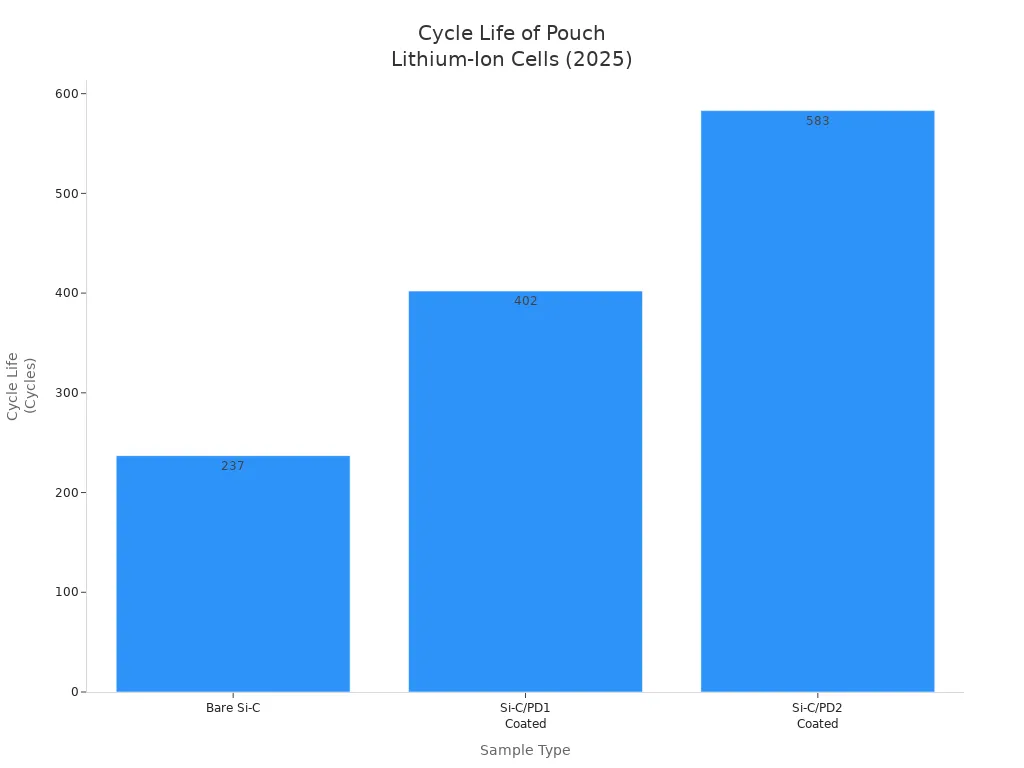
When comparing pouch cells to other formats:
- Prismatic cells have the longest cycle life. Their strong structure and better thermal management help them last longer.
- Cylindrical cells offer more cycles than pouch cells but fewer than prismatic cells. They are reliable and easy to manufacture.
- Pouch cells provide weight savings and cost benefits but have the shortest cycle life due to swelling and less robust structure.
Remarque : Prismatic LiFePO4 pouch cells are popular for long-term use because of their extended lifespan, but pouch cells remain a top choice for applications where weight and space matter most.
Fast Charging
Fast charging is a key area of progress for pouch cells in 2025. New materials and designs help these cells charge much faster without losing performance or safety. Some of the latest advancements include:
- Single-wall carbon nanotubes in the positive electrode boost electrical conductivity and reduce overpotential, which helps prevent lithium plating during fast charging.
- Laser ablation on the negative electrode lowers resistance and improves lithium-ion movement, making charging faster and safer.
- Dual-layer negative electrodes with different particle sizes reduce polarization and improve charge rates.
- High-nickel NMC cathodes increase conductivity and lower overpotential at high charge rates.
- Advanced electrolytes and porous separators further improve fast charge performance.
Manufacturers like DESTEN have developed pouch cells that can charge at rates up to 10C, reaching full charge in 10–15 minutes. These cells maintain high capacity retention, even after hundreds of fast charge cycles. Independent tests confirm that these lifepo4 pouch cells perform well and stay safe under extreme conditions, such as high temperatures and crushing.
- Fast charging rates: 4C to 10C (full charge in 10–15 minutes)
- High capacity retention: ~84% after 800 cycles at 5C
- Validated safety and reliability in third-party tests
Safety Aspects
Battery safety is a top priority for pouch cells. Manufacturers use several safety features to prevent hazards like thermal runaway, fire, and swelling. One important feature is the Safety Reinforced Layer (SRL), which sits between the aluminum current collector and the cathode. This layer stays conductive during normal use but quickly increases resistance if the temperature rises above 100°C or if a short circuit occurs. This action stops current flow and prevents overheating.
The SRL makes up less than 0.5% of the cathode weight, so it does not affect battery performance. Tests show that the SRL reduces explosion rates by over 50% and delays thermal runaway by about 300 minutes. It also lowers the peak temperature during a failure, which helps reduce fire damage. Other safety features include:
- Thermo-responsive polymers in the electrolyte and separator, which block ion flow when heated.
- Positive temperature coefficient (PTC) materials that interrupt current during overheating.
- External devices like pressure valves and fire extinguishers, though these are less effective than internal features.
Common safety incidents for pouch cells include swelling, venting, bursting at low pressures, and thermal runaway. These problems often happen during overcharge or short circuits. Unlike cylindrical cells, pouch cells do not have built-in safety devices, so they rely on external protection and careful system design. Lifepo4 pouch cells are less likely to catch fire, but they can still swell or vent if abused.
Battery safety in pouch cells depends on both internal safety features and careful system integration. Regular monitoring and protection circuits help prevent most incidents.
Thermal Management
Thermal management keeps pouch cells at safe and efficient temperatures. Good thermal control improves performance, battery safety, and cycle life. Pouch cells use both active and passive cooling methods:
- Active cooling: Liquid cooling with special flow channels removes heat quickly. This method is common in electric vehicles. It keeps battery temperatures stable and prevents hot spots.
- Passive cooling: Phase change materials (PCMs) absorb heat as they melt, keeping temperatures even. PCMs work well in compact systems and do not need extra energy.
- Hybrid systems: Combining liquid cooling, PCMs, and honeycomb fins increases heat transfer and keeps temperatures uniform.
Engineers also use heat pipes and tab-cooling to manage heat in high-demand applications. Tab-cooling targets the hottest parts of the cell, improving cooling efficiency and extending battery life. The table below compares different thermal management methods:
Thermal Management Method | Principaux résultats | Quantitative Improvements |
---|---|---|
Tab-cooling with highly conductive ceramics | Superior thermal performance at high discharge rates; effective heat dissipation in tab area; higher cooling performance-to-weight ratio | Equivalent full cycle (EFC) lifespan improved by 8–13% at 5C discharge rate; EFC-to-weight ratio improved by 4–6% compared to no-tab cooling |
Fin-thickness method | Less effective cooling compared to tab-cooling | N/A |
Air cooling | Inexpensive and simple but poor cooling performance | Cooling capacity much lower than liquid cooling |
Liquid cooling | Compact and efficient; widely used in EVs; risk of electrical shorts requires indirect cooling designs | Cooling capacity approximately 9 times higher than air cooling |
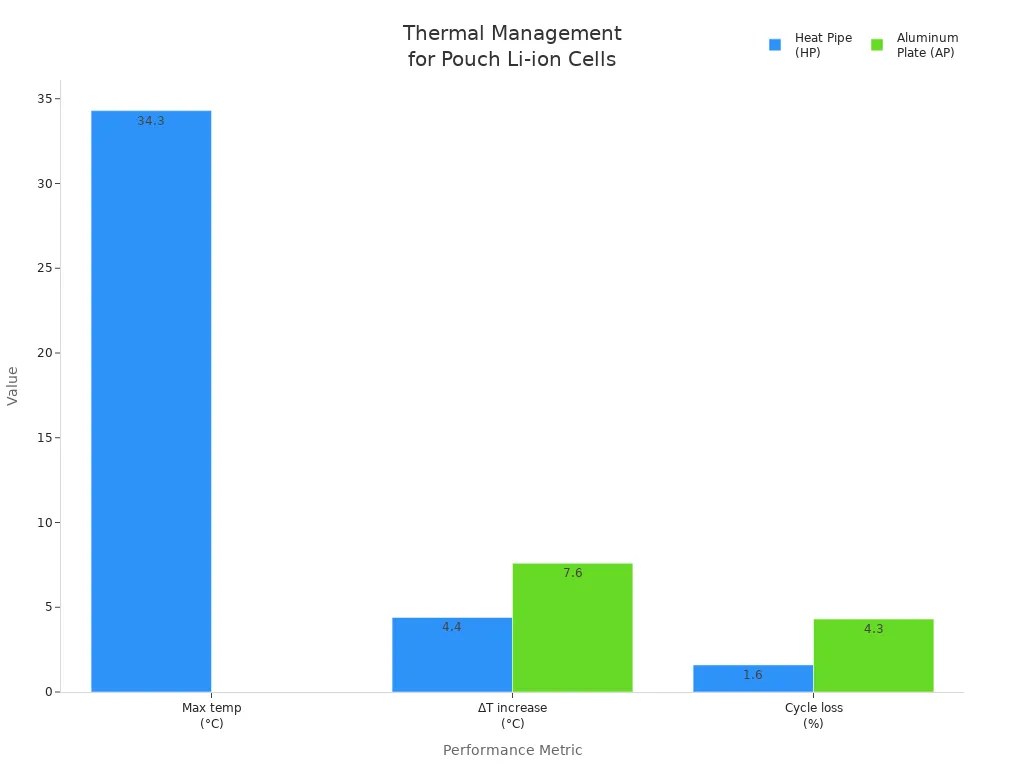
Heat pipe-assisted cooling keeps maximum temperatures stable and reduces thermal gradients, which helps maintain performance and reliability. Hybrid cooling systems, such as those using both heat pipes and PCMs, work well even in extreme environments. Lifepo4 pouch cells benefit from these advanced thermal management strategies, which help prevent overheating and extend cycle life.
Effective thermal management is essential for battery safety, performance, and long-term reliability in pouch cells, especially in electric vehicles and high-power devices.
Pouch vs. Prismatic vs. Cylindrical
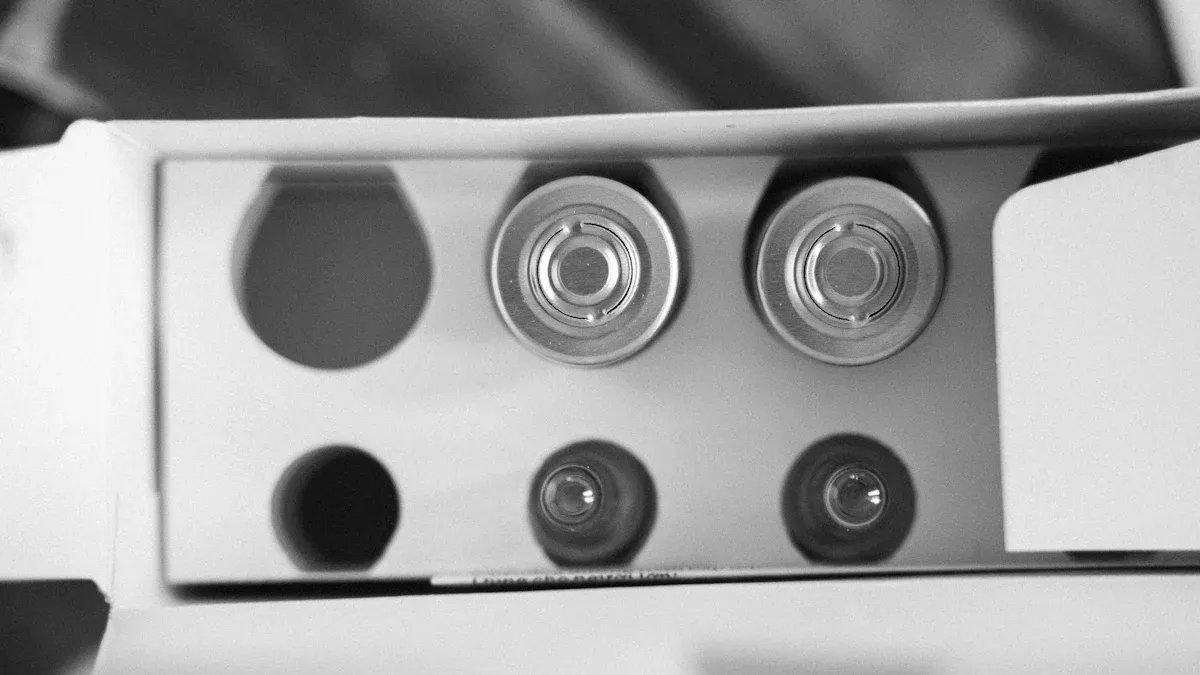
Densité énergétique
Energy density measures how much energy a battery stores in a given weight or volume. Pouch cells often lead in energy density because their flexible design reduces extra materials. This means more active material fits inside each cell. Prismatic cells also offer good density, but their metal casing adds weight. Cylindrical cells have lower energy density due to their round shape and thicker casing. High energy density helps devices run longer and makes electric vehicles lighter. Many engineers choose pouch cells for projects where space and weight matter most.
Safety Comparison
Safety remains a top concern for every lithium-ion battery format. Each cell type has unique safety features and risks. The table below compares the main safety characteristics:
Cell Type | Safety Characteristics | Thermal Management | Structural Concerns and Impact on Pack |
---|---|---|---|
Cylindrique | Round shape allows even distribution of electrolyte and internal pressure, reducing risk of leaks, bloating, or rupture. | Better thermal management due to airflow between cells, allowing quick heat dissipation. | Less impact on pack if one cell fails; pack continues to function as capacity is limited by lowest cell capacity. |
Prismatique | Rectangular shape with steel/aluminum casing; corners prone to stress from shocks and vibrations, increasing risk of deformation. | Poorer thermal management as cells are stacked closely, limiting airflow and heat dissipation. | One bad cell can affect the entire pack due to series stacking and close contact between cells. |
Pouch | Soft plastic film enclosure instead of rigid casing; design noted but detailed safety implications not fully described. | N/A | N/A |
Pouch cells can swell if damaged or overcharged. Prismatic cells may deform at the corners. Cylindrical cells handle pressure well and often show the best safety record in harsh conditions.
Cost Factors
Cost-effectiveness plays a big role in choosing a lithium-ion battery format. Material costs, especially for cathodes like NMC811 and LFP, make up most of the expense. Equipment for making cells, such as coating machines, adds to the cost but less than materials. Pouch cells use less casing material, which can lower costs. However, if pouch cells have lower areal loading, they need more passive parts and more equipment, which can raise costs. Location, energy, and labor have smaller effects on total cost. Political support or subsidies may help reduce costs further. In general, pouch cell cost factors match those of other lithium-ion battery types.
Adéquation de l'application
Each cell type fits different uses. Pouch cells work well in electric vehicles, drones, and thin electronics because of their light weight and flexible shape. Prismatic cells suit large battery packs for buses and energy storage systems. Cylindrical cells power tools, e-bikes, and some cars because they are strong and easy to cool. Engineers look at energy density, safety, and cost-effectiveness when picking the right cell for each job.
Tip: Choosing the best cell type depends on the needs of the device. Pouch cells offer advantages in weight and density, while cylindrical cells provide strong safety and reliability.
Market Trends in Lithium-Ion Battery
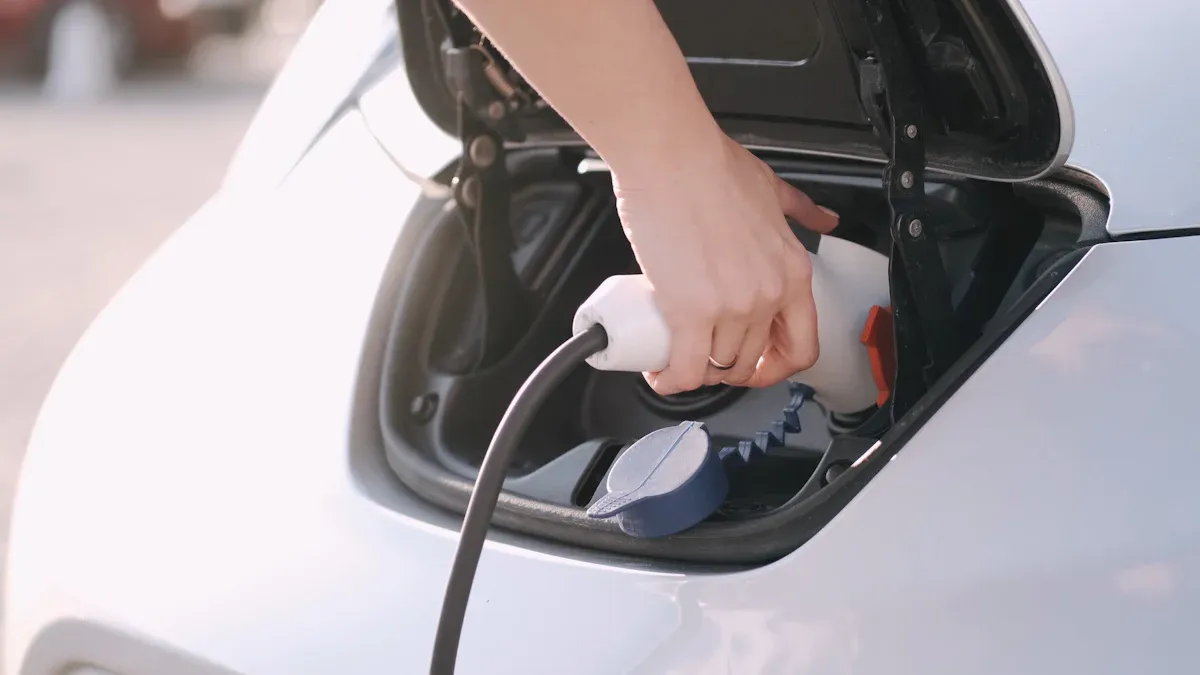
Adoption in EVs and Electronics
In 2025, automotive companies increase their use of pouch lithium-ion batteries in electric vehicles. Government rules and incentives push this trend forward. These batteries help cars drive farther and charge faster. Electric vehicles now drive most of the demand for pouch cells. By 2027, experts expect electric vehicles to use over 60% of all pouch cells made. The global production capacity for pouch cells reaches about 1.5 billion units each year, with most going to the electric vehicle sector.
Consumer electronics, such as smartphones, laptops, and wearables, still use pouch lithium-ion batteries. People want lightweight devices with long battery life. However, the share of pouch cells in electronics drops as electric vehicles and energy storage systems grow. The Asia Pacific region, especially China, leads in both making and using these batteries. Strong government support and investments help this growth.
Innovations in 2025
Manufacturers introduce several new technologies for pouch lithium-ion batteries in 2025:
- NEO Battery Materials uses a one-step nanocoating on silicon anodes. This process helps batteries last longer and charge faster.
- Batene replaces traditional foils with fleece current collectors. This change increases energy density and safety.
- SONOCHARGE applies acoustic wave technology to improve lithium ion movement and reduce harmful dendrites.
- Nanoloy uses plasma printing to make batteries with stronger bonds, which delays battery aging.
- Vocai adds on-chip gas sensors for better battery management and safety.
Other improvements include flexible sizing, lightweight construction, and better heat distribution. These changes make pouch cells more durable and efficient.
Regional Market Dynamics
Région | Key Trends and Drivers | Market Share / Focus | Supporting Factors and Notes |
---|---|---|---|
Asia-Pacific | Fastest growth; strong manufacturing; government incentives | China ~60% global production | Large EV market; leaders like CATL; focus on recycling and sustainability |
L'Europe | Big investments in local battery production; policies for supply chain localization | Growing production capacity | Efforts to reduce reliance on Asia; innovation hubs, especially in Germany |
North America | More investment in battery plants; focus on local supply chains | Expanding capacity | Policies for domestic production; partnerships for advanced battery technologies |
All regions see more use of LFP chemistry and higher energy density cells. Demand from electric vehicles and energy storage solution projects continues to rise. Companies also focus on recycling and second-life uses to improve sustainability.
Battery Manufacturing Challenges
Swelling and Stack Pressure
Manufacturers face major challenges with swelling and stack pressure in lithium-ion battery cells. Lifepo4 pouch cells can swell up to 10% in volume after many charge cycles. This swelling happens because gas forms inside the cell during charging and discharging. The swelling puts stress on cell parts, such as welds, and can cause damage. To control this, engineers use springs or other devices to apply steady pressure. They must keep the stack pressure between 3 and 8 psi. If the pressure is too low, the cells may swell too much. If it is too high, the cells may get damaged. Over time, the cells grow by 11–13%, so the pressure system must adjust. Constant pressure fixtures, like springs or pneumatic systems, work better than fixed plates. They keep the pressure steady and help the battery last longer. However, these extra parts take up space and lower the energy density advantage of lifepo4 pouch cells. Heat transfer plates are also needed for cooling, which further reduces space efficiency.
Durability and Damage Risks
Durability is a key concern for battery cells. During manufacturing, tiny metal particles can get inside the cells. These particles may cause short circuits, which can lead to thermal runaway. Thermal runaway starts when the cell temperature rises above 130°C. It can cause the cell to vent hot gases or even catch fire. This risk can spread to nearby cells and cause a chain reaction. Lifepo4 pouch cells need careful handling during vacuum evacuation, electrolyte filling, and pressing. Chemical hazards include flammable solvents and explosive dust. Factories use fire-resistant materials and separate storage areas to improve safety. There are no complete public guidelines for all safety steps, so each company must follow best practices.
Supply Chain Issues
The supply chain for battery cells faces several problems. Raw materials, such as lithium and cobalt, can be hard to get and expensive. Shipping delays and shortages can slow down production. Recycling and end-of-life management add more challenges. Used cells must be collected, tested, and processed safely. This process costs money and needs special equipment. Companies look for cost-effectiveness by improving recycling methods and using safer materials. Lifepo4 pouch cells offer better safety and longer life, which helps reduce waste and lower costs over time.
Pouch cell technology in 2025 offers high energy density, flexible design, and strong performance for many applications. The advantages of the pouch cell include lightweight structure and easy customization. Manufacturers and buyers should consider factors such as chemistry type, cycle life, safety features, voltage, and operating temperature range when choosing a battery.
The market for pouch cells will keep growing, with new innovations like solid-state batteries and smart energy systems. These changes will help meet the rising demand for safe, efficient, and adaptable batteries.
- Choose pouch cells for devices that need light weight, high energy, and custom shapes.
- Always match battery features to the needs of each application.
FAQ
What makes pouch lithium-ion batteries different from other types?
Pouch cells use a soft, flexible casing instead of a hard metal shell. This design makes them lighter and easier to shape. Many engineers choose pouch cells for devices that need custom battery sizes.
How safe are pouch lithium-ion batteries?
Pouch cells include safety layers and special materials to prevent overheating. They can swell if damaged, but they rarely explode. Engineers add protection circuits and monitor the batteries to keep users safe.
Can pouch cells be recycled?
Yes, companies can recycle pouch lithium-ion batteries. They remove valuable metals like lithium, cobalt, and nickel. Recycling helps reduce waste and saves resources. Many countries now require battery recycling programs.
Why do pouch cells swell over time?
Gas forms inside the cell during charging and discharging. This gas causes the pouch to expand. Engineers use pressure systems to control swelling and keep the battery working well.
Where do people use pouch lithium-ion batteries most?
People find pouch cells in electric vehicles, smartphones, laptops, and drones. The light weight and flexible shape make them a top choice for many modern devices.